In June, KOCH Industrieanlagen GmbH held its demonstration day at the company headquarters in Dernbach, Germany. PRO Flexconvert was on-site live and spoke exclusively with Jan-Henning Röseler, Business Development Manager Converting.
Mr Röseler, we are meeting today at the KOCH Demonstration Day. What significance does this event have for your company?
Jan-H. Röseler: Demonstration days are very important for us. We have realised that often not all interested customers show up at trade fairs, even though they have a current need. In addition, there is usually not enough time for in-depth discussions. Our demonstration days, on the other hand, offer the opportunity to talk in-depth with customers about their experiences, future plans and needs. Our experts from the fields of system planning, engineering, electrical engineering for software and hardware as well as after-sales service are available to answer any questions. This enables us to find out what is important to our customers and where they would like to see improvements. Another advantage of our demonstration days is that, unlike at trade fairs, customers can see the systems live. Depending on the current industry focus, we issue targeted invitations, which is confirmed by the response: numerous customers and interested parties gladly accept our invitations. These events take place at least twice a year, with the next demonstration day planned for the autumn. Interested parties and customers can register for our KOCH demonstration day via our website and will receive information as soon as the date is finalised. In short: a win-win situation for visitors and us.
A number of systems are set up here on site today – ideal for demo purposes . . .
J.-H. Röseler: We always set up the systems here in the form of interfaces. Some of the overall lines are extremely large – but we don’t have to build a 50-metre conveyor line, for example. Instead, it’s all about the centrepieces, the most important parts: we need to know how a gripper works, how the processes harmonise with each other and what happens in detail while a product is being manufactured.
What exactly is KOCH focussing on during the current demonstration day?
J.-H. Röseler: We have shown some real highlights today – including the handling of large rolls of film and paper. We also demonstrated our patented KOCH RobotFlexPacker roll packaging machine in a fully automatic cycle with double packaging. We are observing a clear trend here, as many customers – for example in the hygiene segment or for food – want to double-pack rolls.
Another system that we are very proud of is a complete commissioning centre for construction chemicals in sacks. This centre can not only palletise bags but also pick them. Orders transmitted from SAP are converted fully automatically into order-specific mixed pallets for products such as tile adhesive and grout, secured, labelled and transported to the loading area ready for dispatch. We successfully realised the first system with SAP interface with the same customer a few years ago, and now the customer has ordered another identical system for an additional production site. This repeated cooperation is a real testament to our work.
Glass is also a major topic for us. There are numerous glass processing companies in the region around Koblenz, and we are currently able to demonstrate a complete automation system from production to palletising. Thanks to the variety of markets we serve, we are able to compensate for market fluctuations quite well.
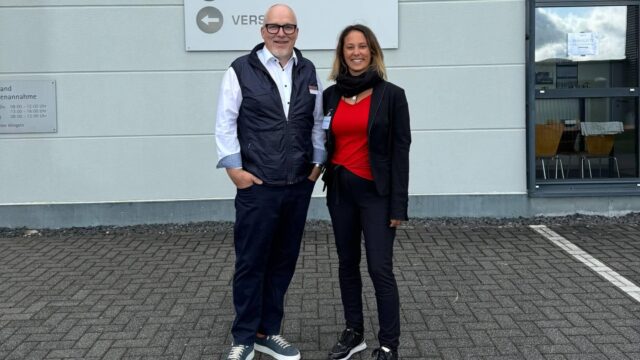
What is the current situation in the converting market in particular?
J.-H. Röseler: The converting market is actually always strong! Those who started with a system at some point want to expand – that’s a big trend at the moment! We are currently working on several projects involving the expansion of existing systems. The packaging machine we showed today is also intended for expansion. We are preparing ourselves for the fact that we will be automating even more for our customers, as this higher degree of automation is being demanded more and more frequently. In the past, systems were built that required manual loading of a magazine. Today, the trend is towards fully automated magazine loading.
Artificial intelligence is therefore also a very important topic for us! It is already being used in our new packaging system. It’s also about virtual commissioning: we want to move away from having to set up the systems twice. Instead, we want to recognise and rule out errors in advance in order to further reduce the time spent on-site at the customer’s premises. We now also simulate complete systems and do a lot of engineering for our customers. This is useful because we want to know exactly what happens at the customer’s site so that we can learn from it. The customer is on board as a partner.
How does KOCH deal with the shortage of skilled labour?
J.-H. Röseler: Demographic change and the shortage of skilled labour are a major issue for all our customers. Anyone who has been somewhat surprised by this development or realises that things can’t go on like this will naturally quickly turn to the topic of automation. However, the 100 per cent solution is not necessarily the right one, because you have to take economic factors and costs into consideration. We can’t completely replace people. We can use camera systems and lasers and give the robot tools so that it can act almost like a human being, but in the end, it is not a human being. That’s why our projects are always designed in such a way that the customer’s economic efficiency takes centre stage.
On the other hand, I stand by the following statement: “If you don’t automate, you lose!” There is a shortage of people in production in particular – and it’s not exactly nice when an employee has to stack tonnes of rolls all day long. It would be a good idea to train this person as a specialist for the slitting machine instead, for example, to control quality and minimise downtime.