Flexography has over time extended its sphere of influence, taking on all comers, enabling the savvy converter to bid for and obtain orders in countless high-value print quality focussed product segments, such as wrap around and shrink labelling; printing and conversion of FMCG and many more besides.
Food, beverage and manufacturers of consumer goods are driven by current business conditions, which are increasingly global in context and which often require an assertive and dynamic approach to methods of marketing and presentation and the processing of innovative and more eco-acceptable substrates, taking into account recyclability and sustainability.
Support technologies
As with many print and industrial processes, quality, speed of output and the ability to accommodate a wide range of substrates without compromise is as much dependent upon support technologies as the press itself. Irrespective of whether the support technology, ancillary or consumable is the ink, anilox roll, photopolymer plate, mounting tape or pre-press colour communication proofing device – each unit, device or component is of equal importance and is relevant to the overall performance of the machine and workflow.
Ink flow, how much ink one puts on the plate and ultimately the substrate can be crucial. Ink film thickness influences quality. For line work, thinner ink films have many benefits. Even when a press has less than perfect dryers, applying less ink speeds up drying, which means faster press speeds. So what can go wrong? Ink that is still wet may pick from the substrate causing transfer to the plate in the next deck. Thin ink films also trap better because of a more even lay-down of the inks. With the smooth, controlled lay of the ink film, not only do large solids appear even and consistent, but the rest of the line work improves as well. Type prints are sharper because the controlled ink layer on the surface of the plate does not build up on the shoulders as easily. Reverse type benefits the most. Given the increasing amount of information that needs to be included on labels and packages, the use of less ink enables small point sizes to be printed clearer with minimal risk of fill-in.
Thin ink film thickness reduces the risk of slur and build up on the plate edges. Too much ink can cause dirty screens. Also, a thicker ink layer on the tip of the dot enables the ink to bridge or connect to the surrounding dots. This is especially problematic in the mid-tone range on process images and gradated screens or vignettes.
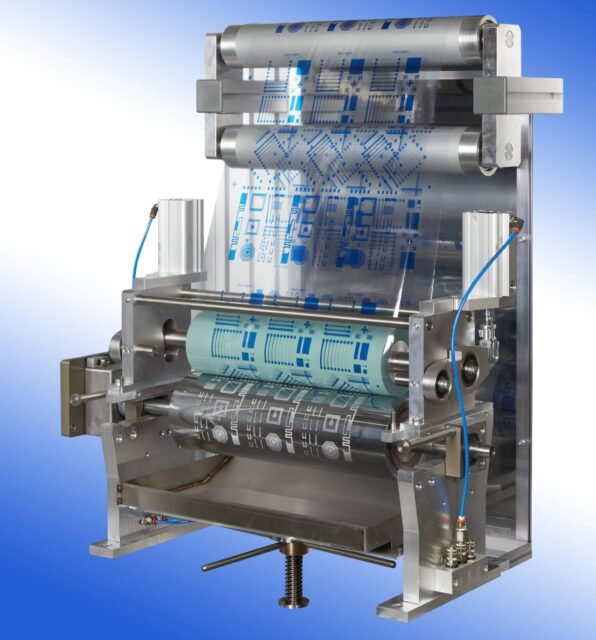
Improved ink mileage
Another benefit realised when running the thinnest ink film is improved ink mileage and thus lower ink costs. One caveat: when switching to a lower volume anilox roll in order to obtain better control of the ink costs can go up as it may be necessary to change ink formulations, moving perhaps to a slower vehicle, one with a higher pigment load and with reduced levels of water or fillers and other inexpensive reducers that bulk out the formulation.
So how can the printer resolve printability issues such as those surrounding the use of thinner inks without tying up the production press for long periods? The ink supplier and anilox roll supplier can provide valuable input while systems such as the FlexiProof 100 or variants FlexiProof UV and FlexiProof LED UV can be invaluable in resolving quality and printability issues and for colour matching and trialling of unfamiliar substrates.
With the FlexiProof one way of determining the minimal but most effective level of ink film is to run various test rolls with several engraving specifications or bands across the face. By mounting and aligning test images with each band, the comparisons help determine the thinnest ink film that can be used without compromising colour quality.
Written by Tom Kerchiss, Chairman of RK Print Coat Instruments Ltd.